The Basics - The Benefits of Optimization Software
What is Optimization?
Consider the following scenario: the XYZ Company wishes to save money on expensive sheet material by designing efficient piece cutting layouts. However, the XYZ cutting line has three saws and it is undesirable for pieces coming off the last saw to be returned to the start of the line for further operations. There is a constraint on the process: the final pieces must be available after a single pass through the line. The tradeoff is that high efficiency layouts can require many saw operations, but the number of saw operations is limited by the cutting line's capacity. Therefore, the efficiency of the layouts is reduced.
Your company may be in a similar situation. To build a given assembly, you must obtain the required pieces by cutting them from multiple sheets of material. What layouts make efficient use of the material? How many sheets are required? How much time should be spent designing the layouts? Optimization software can help you determine effective answers to these questions.
Optimization minimizes the cost of a process with respect to its constraints. In the context of the above situation, the process is cutting pieces from sheets of material. The cost of this process is the amount of sheet material consumed and time. You and your shop set the constraints. These are determined by equipment and labor capabilities, the desired workflow through the shop, or assembly-specific details.
Optimization software is a tool that lets you specify the list of pieces to be cut, the available sheet material, and the constraints on your process. The software analyzes the tradeoffs to be made and produces an efficient set of layouts that meet the constraints. In the remainder of this article, we'll use this software to save sheet material, reduce layout design cost, and perform "what if" analysis to improve your cutting process.
A Demonstration
To illustrate the benefits of optimization software, we will use "The ITEMIZER" from R&R Drummond, Inc., and consider the demonstration cutting list shown in figure 1. The constraints are shown on the top half of the screen, and the list is on the bottom.
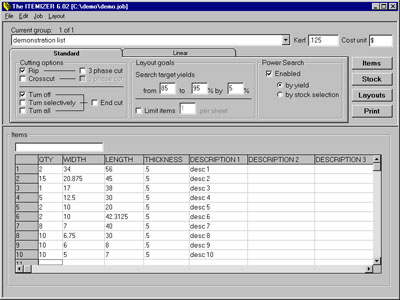 Figure 1. Example Cutting List
The demo list contains ten unique piece sizes (items), with varying quantities. We will use this list to show how different constraints affect material efficiency and total cost. The first set of constraints specifies the cutting options as "rip, turn off". This means that the layouts developed by the software will run with the length of the sheet and pieces will be oriented as shown in the list (rotations are prohibited by this option). The target yield and power search options are set to provide a wide variety of candidate layouts.
For sheet material, we will assume that both 4x8' and 5x12' sheets are available. The layout efficiency benefits from a variety of sheet sizes, as the software can choose the best sheet size for the pieces at hand. Both sheet sizes cost $10/sq. ft.
Figure 2 shows the layouts generated by the software. The optimization took about two seconds to execute, which illustrates one of the main benefits of optimization software: drastically reduced design time. Since each set of constraints takes seconds to execute, many cutting options can be analyzed in a fraction of the time it takes to design layouts by hand. In addition, the numbered and labeled layout drawings can be immediately printed or exported to DXF format to produce high-quality cutting diagrams for the shop.
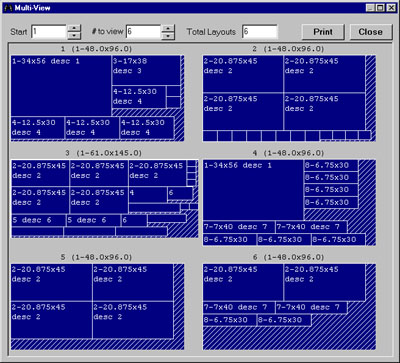 Figure 2. Rip-turn off layouts: 84.9% yield, cost $2,214
With these basic constraints, we use 84.9% of the sheet material (yield) at a cost of $2,214. Note that the software chose to use five (5) 4x8' sheets and a single 5x12' sheet. To see how these figures can be improved, let's remove some constraints by setting the turn option to "turn selectively" and selecting "3-phase cut". Turn selectively allows the software to rotate pieces by 90 degrees in order to achieve higher yields. Three-phase cutting will allow pieces to be placed across the initial rip lines, which will require a cutting sequence of rip-crosscut-rip, hence "three phase" cut. Note that these constraints are much less stringent than our original settings, which prohibited turned pieces and the crossing of rip lines.
The result is shown in figure 3. The new constraints allow an increased yield of 87.6% and they reduce the material cost to $2,162. So, for a few seconds (literally) of optimization time, $52 is saved in material cost. This is a small example: when either the sheet cost or job size increase, so does the amount of money saved. This time, the software chose three (3) 5x12' sheets and a single 4x8' sheet. Of course, the choice of constraints is up to your shop. If you're cutting a grained material, you might require a fixed grain direction on each piece. In that case, turned pieces would be prohibited.
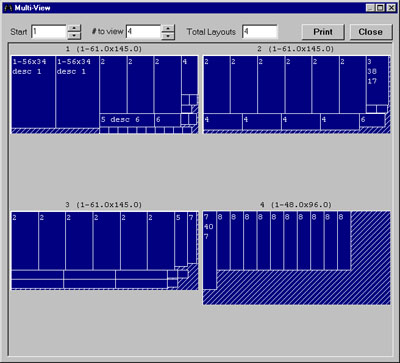 Figure 3. Rip-turn selectively-3 phase cut: 87.6% yield, cost $2,162
Optimization software also can help determine the cost vs. benefit of changes to your workflow. Although it's more efficient, three-phase cutting may not be permitted by the setup of machinery in your shop. But consider this: if three phase cutting were possible, would you save enough money in the long term to justify reconfiguring your cutting process in the form of additional equipment, training, or personnel? The answer depends on your specific situation, but an extra three percent of saved material can add up quickly, particularly if your cutting volume is high and your material is expensive.
Cost vs. Yield
High material efficiency (yield) does not always provide the lowest total cost when there is a difference in the cost-per-square-foot of your sheet material. This is illustrated by figure 4, which shows two plots. Each data point represents a particular set of layout constraints, chosen to achieve the yield value on the x-axis of the plot. The y-axis shows the material cost in hundreds of dollars.
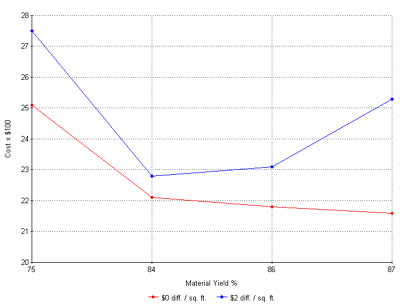 Figure 4. Cost vs. Material Yield
The top curve plots material cost vs. yield in the case where there is a $2 difference in the square-foot cost of our sheet material. In the context of our specific example, our 4x8' sheet costs $10 / sq. ft., and the 5x12' costs $12 / sq. ft. The curve on the bottom plots cost vs. yield where both sheets cost $10 / sq. ft.
Notice that the bottom curve always decreases as material yield increases. This is the result of the uniform sheet cost. In this case, material area and total cost are one and the same, so to reduce one is to reduce the other. The software can choose the best sheet sizes to get the highest yield. The top curve behaves differently, however. Beyond 84% yield, the total material cost goes up, as the software uses more of the 5x12' sheets to improve the yield. In this example, the optimization software shows that it is more cost effective to buy more of the small sheets (lower yield), instead of buying less of the larger ones (higher yield). Refer to figures 2 and 3, which show that the lower-yield layouts used more 4x8's. The higher yield layouts used fewer sheets overall but used mostly the higher cost 5x12's.
Choosing the Right Software
When shopping for optimization software, go to the Web and download demo applications if they are available. This is the best way to evaluate what a piece of software can do. After installing a demo, your first tendency might be to see how many pieces the software can pack on a given sheet. Feel free to do just that, but you should also rate these important areas: ease of cut list entry and quality of printed output.
If you already enter your cut lists into another application, such as a spreadsheet, make sure that the optimization software is able to import the cut list from your current application. The import mechanism might be simple cut-and-paste or some type of common file format, but in any case this import feature will save you a lot of retyping.
The printed layout drawings are ultimately what your operator uses to cut the pieces. To get the most out of the software, the printed drawings should be clear and easy-to-read. The sheet dimensions, saw kerf, and the layout's cut list should be printed on the layout drawing so that all of the required information is present in one place.
Summary
Optimization software can help you make the right decisions in order to save time, material, and money from your cutting process. The choice of cutting constraints has a significant effect on material efficiency (yield). These constraints, which include settings such as cutting style and piece turning allowances, are specific to your shop's cutting process. Although material efficiency is desired in general, material cost must also be taken into consideration. Optimization software, such as The ITEMIZER from R&R Drummond, Inc., is a tool for quickly comparing the tradeoffs between cutting constraints, material usage, and overall material cost.
Written by Ryan Drummond, VP Product Development, R&R Drummond, Inc., creators of The ITEMIZER panel cutting optimization software.
For more information, or to download a demonstration version of The ITEMIZER, go to R & R Drummond's website at www.rrdrummond.com or contact them at R&R Drummond, Inc., 10 Pike Street, Herminie, PA 15637, Ph/Fax 724-446-0159, e-mail: rr@rrdrummond.com.
|