ROUTING: Trimming Thermoformed Parts
Proper tooling, fixturing, pressure and speed are necessary when using CNC or air routers to trim formed parts.
Use of router bits during the production of thermoformed plastic parts is one of the oldest applications of router tooling in plastics. Almost since the inception of pressure forming and vacuum forming, router tooling has been used to remove flashing, separate parts and create holes or cutouts.
The earliest plastic application router bits were designed to facilitate hand operations and reduce operator fatigue in repetitive operations such as part trimming and cutouts. With the advent of 5-axis CNC routers, the tooling has evolved into specialized bits to reach deep into cuts and prevent part movement on large, single-piece components. This article will highlight the differences between the two styles (manual and CNC) of tools and provide information on their selection, application and use.
Tooling
Most thermoformed parts are made of softer materials that react well to O-flute style tooling. In air router applications, the most common choice has been single edge and double-edge straight tools. Single-edge tools typically feed the easiest and double edge tools will usually give a better finish and allow faster feed rates in the hands of an experienced operator.
Typically, high-speed steel (HSS) is the material of choice in air routers due to its ability to withstand impact and its grinding characteristics that allow a sharper edge than solid carbide (SC) after machining. These properties lend themselves to use in environments where tool breakage and operator fatigue are common. Other features common to hand tooling for use in thermoformed parts are the extended shank and cutting edge lengths. Extended shanks allow for a larger colleting area and an additional surface for internal guide bearings to ride on. This improves tool rigidity and helps to reduce cutter breakage while improving the overall "feel" of the routing operation. The extended cutting edge length gives extra cutting area past the nose bearings and allows the operator to present the router bit to the material without having to remove any safety or guide components from the router head.
With the increased use of CNC 5-axis machines to trim parts, the viability of SC has seen a large increase when compared to its use in air routers. The improved repeatability and constant feed rates of these machines versus hand routing has allowed the increased stability and rigidity of SC to produce faster feed rates and improved edge finishes, without the vibration associated with HSS. As with HSS, SC tooling for trimming is typically sold with extended cut lengths and shank lengths. The longer
shanks are used for reach when trimming complex mold parts that may require the router head to maintain a longer than normal distance from the part due to interference. The longer cut lengths are used to ease the programming of difficult contours and cutouts. Because of factors relating to router head orientation and interference, it is not atypical to present a cutting edge to a trim surface at something other than a perpendicular angle. By having a longer cut length to cut this larger area, a shorter, simpler program can be generated.
The use of CNC machines has also led to additional geometries beyond straight O-flutes
being successfully applied to the trimming of thermoformed parts. SC low-helix spirals have
seen success in both single-edge and double-edge configurations. Typically these spirals are of an O-flute or modified O-flute style and will be used with an upcut helix when the parts are thicker than 0.090 inch and have a solid fixturing. If part movement or chatter is present, a downcut can be used to increase the effectiveness of the router fixture and improve part edge finishes.
CNC Fixturing
Solid, effective fixturing is one of the fundamental keys to successful trimming operations. More often than not, an improvement in hold-down capability can do more to improve a trimming operation than adjusting feed parameters, picking the optimum tools and tweaking program parameters combined.
The material from which the CNC fixture is formed is the best place to start when examining the capability of a routing operation. While plywood is one of the best materials to use, its cost for construction time can be difficult to justify. A poured urethane foam base can also be expensive, but its ease of use is usually a benefit to shops without a dedicated mold and fixture department. The drawback of poured fixtures is their susceptibility to dimensional instability and occasionally poor rigidity, depending on their construction.
The key to an effective fixture is the ability to distribute its holding power over a large area as well as specifically reaching the edges where routing operations are to take
place. The single biggest failure of fixtures is their inability to supply adequate vacuum where it is needed. Good forethought in the design phase of a fixture will ensure adequate room to run internal piping and vacuum supply to the edges of the areas to be routed. When the configuration prevents internal vacuum supply from reaching an area, the next best method is to use deep vacuum supply channels on the top surface of the fixture to distribute vacuum throughout the cutting area.
In instances where the part/fixture interface is an irregular fit (inconsistent parts, poor fixture design or poor alignment), good gasketing is essential for retaining vacuum pressure at the cutting interface. A good gasketing material will be either a low durometer, flexible, dedicated gasket material or a closed-cell, crush-resistant foam
tape. Weatherstripping is not an acceptable gasketing material due to its low bond strength adhesive in lateral-stress applications and its inability to recover from repeated stress and compression cycles.
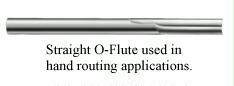
Air Routers
Hand air routers work well in trimming thermoformed parts when the router is new or well maintained and the setup of the router is done correctly. If the setup is not done correctly, the resulting trimming operation will have built-in wastes of both time and tooling.
Air routers, as most machines, wear out over time with normal use. The hard part is determining when to perform maintenance and repair. The manuals should note the maintenance frequency recommended by the manufacturer, which should be the first point of reference. If a manual is not available, or a maintenance schedule is not found, here are some tips for repair and maintenance for air routers.
1. The item most overlooked and first to need repair in an air router is the front nosepiece bearing. The estimated useful life of this bearing is 100 hours. For most operations, this could be one to two weeks of use. Depending on the materials cut, the life may be longer or shorter. The bearings in the nosepiece are normally shielded bearings and not sealed. Often the chips and dust from the trimming operations find their way into the bearings and cause premature wear. The router motors also should be inspected after 500 hours or sooner and repaired after 1,000 hours to ensure proper performance.
2.One of the more overlooked essentials in proper setup of a hand air router is the air pressure at the point of use. The easiest way to ensure the proper air pressure and air volume is to install a gauge at the point of use. With a gauge in line at the point of use, the router should be placed under load and the gauge readings verified to a recommended steady pressure range of 90 to 100 psi. Under normal use, the pressure can be watched to ensure the router is operating within the recommended pressure range at all times.
Air pressure and volume are to an air router what volt-age and amperage are to an electric router. If the pressure drops below 90 psi when under load, it could be a sign that the air feed line is too small or the overall volume of air is under capacity. Solutions include installing larger feed lines and/or adding an air tank nearby to act as a supply capacitor to the system. The impact of low pressure or low air volume is lower speed (rpm) and reduced horsepower, resulting in more difficult cutting and extra tool wear. Lower speeds can slow production, resulting in longer times and higher costs to produce the same parts.
CNC Routing
Once the proper tools have been selected and a solid fixture built, the last factor to consider when routing thermoformed parts on a CNC 5-axis router is the router itself. Proper programming and feed and speed selection will determine the viability and profitability of an operation.
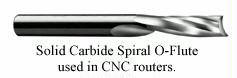
The greatest advantage of a CNC router over hand routers is the increased feed rates attainable and the improved consistency of the finished part. With multi-flute,
plastic-specific tooling and solid fixturing, feed rates of 250-350 ipm are attainable in 5-axis trimming and cutout operations. Lower feed rates are typically required when
general-purpose router tooling and poor fixturing are utilized. Most often, these problems manifest themselves as inconsistent chatter marks in poorly fixtured areas, such as corners or extended, overhanging flashing.
Programming for optimum finishes and speed should take into account not only feeds and speeds, but also cutter entry locations and angle of presentation of the cutting edge to the workpiece. When router bits enter a softer working material, they will often "walk" or enter in an eccentric spiral configuration. This is the result of the point geometry being ground to produce flat cutting bottoms and the lack of a center-pointed drill tip to keep the cutter’s entry concentric. The best method to eliminate evidence of a spiral entry is to plunge the cutter in an area of scrap and then rout to the cutaway area perimeter. This applies both to flash trimming and cutout or interpolated hole work.
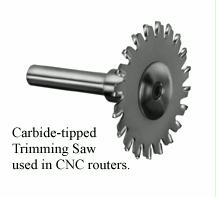
An additional concern when programming for 5-axis work is the orientation of the cutting edge to the work surface. Router bits are designed to be run perpendicular to the surface being cut and any misalignment can lead to increased instances of cutter breakage or chatter. While
5-axis tooling is designed to handle these increased stress loads and the cutting edge lengths are intentionally elongated to compensate for the increased effective depth of cut, the best method is still to provide extra time during the programming phase to keep the router head
oriented perpendicular to the cut plane.
Using routers for trimming thermoformed plastic parts has been, and will continue to be, one of the best methods of separating finished parts from extra forming material. As CNC 5-axis machines become more popular, the attention paid to cutter selection, router and fixture rigidity and programming will have to increase in order to maintain profitability. The best method is to analyze the process early in the development cycle and plan for necessary factors, instead of attempting to improve poor fixtures or programs after their creation.
For more information, click on the Author Biography link at the top of this page.
|