ROUTING: Routing & Fixturing ABS
The fixturing
method, feed rate
and chip flow control
can determine the
type of tooling used
when machining
ABS.
ABS is one of the most popular plastics
used by thermoformers
and rotational molders. It is
also one of the most versatile,
from low-density foam to highdensity
material. It has been
used in consumer products for
years and is becoming the
material of choice in many auto
and truck components.
ABS combines toughness, stability,
wide temperature range and
chemical resistance with relative ease
of fabrication. That, combined with its
low water absorption and high to low gloss
range in a variety of colors, often makes it the plastic
formula of choice for a wide range of
applications.
Instrument panels, headliners,
grilles, wheel covers, decorative
trim, mirror housings, truck bed
liners and bumper farings are
some of the applications in
which ABS has been used successfully.
Small and large appliances,
refrigerator door liners,
business machine and electronic
housings, luggage, toys, storage
bins and flower pots also made from
ABS are often trimmed by air or CNC
routers. Pipe and fence materials made from
ABS are used in several products requiring unique
routing methods.
Using a Spoilboard
ABS is a reasonably-priced material
and can be machined in a most
cost-effective manner. While the
substantive properties of this material
would often dictate restrictive
machining practices in other formulations,
this is not the case with
ABS. There are just a few — but
important — considerations when
routing or trimming ABS.
In many instances, CNC routers are
set up with the right tools and an
elaborate vacuum system. The spoilboard,
however, is overlooked and
becomes the problem area. The one
thing that can make or break an ABS
setup is the ability to hold a part on
the table “rock solid.” ABS parts are
normally quite flexible and will tend
to vibrate if not fixtured properly.
There are many elaborate pod systems
employed by both point-topoint
machines and routers. These
systems can be very effective. There
are also many machines utilizing
dedicated spoilboards to hold parts.
This is most often the case with ABS
parts. The proper way to build a dedicated spoilboard is often misunderstood or cut short, in
the interest of time. Taking the time to do it right will pay
dividends in the form of productivity and piece part finish.
Many people consider a spoilboard a piece of MDF or
particleboard with self-stick weather-stripping and a few
holes drilled inside the perimeter. While this type
of fixture may work in a few instances, it does not
often satisfy the demands made in high-performance
routing. If a router is going to run at production
speed, the parts must not move. The preferred
spoilboard technique employs grooving the
interior area of the gasket perimeter to allow a
vacuum to reach the outermost portion of the
part. The holes are then drilled at the intersection
of the vacuum grids.
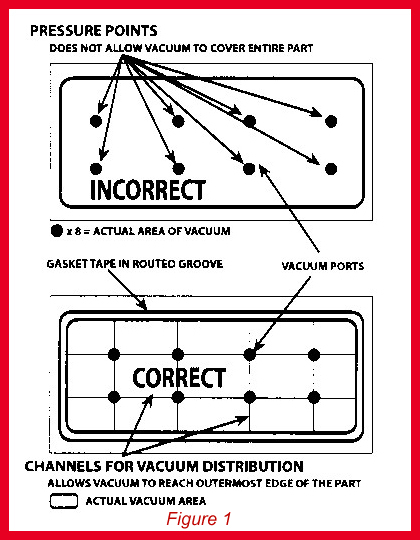
The method provides a
greater vacuum surface area. It is preferred to
just drilling holes in the spoilboard because it provides
a “bead” of vacuum to the outermost edge
of the part, giving the best chance for a “rock
solid” hold. (Figure 1)
Tool Selection
Once the ABS has been properly fixtured, tool
selection is a straightforward process. The router
bit of choice for most thermoformed sheet, 6mm
or less, is the O flute tool, either single or double
edge.
In many instances, the part can be machined
while cooling. High-speed steel tools work very
well in this instance. (Figure 2) In all instances,
ABS can be trimmed and routed effectively with solid carbide O flute tools. (Figure 3)
A newer product in solid carbide router bits for plastic applications is the O flute spiral
tool. (Figure 4) While available for many
years in straight or shear geometry,
recent developments in CNC grinding
technology has enabled the design and
manufacture of the O flute spiral,
which provides for better chip flow
control in certain applications.
Reweldment
One of the few problems in
machining ABS can be chip
reweldment. This occurs when
the chip is not removed properly
or quick enough. It can
also occur when the feed rate
is too slow.
While these problems can
be easily resolved in a CNC
environment with proper fixturing
and tool selection,
they can be more difficult to
solve in hand-held or air routing applications.
Depending on the difficulty of the setup, fabricators
may want to consider using carbide-tipped
straight flute tools if high speed steel
does not provide satisfactory tool life. (Figure 5)
In these situations, carbide-tipped tools may be
preferable to solid carbide because of the
strength of the tool steel body. Whether the
router is CNC or hand-held, ramp entry into the
ABS workpiece — rather than straight plunge
— will also prevent rewelding.
In any plastic routing application, fabricators should
experiment with both single- and double-edge bits, as
well as both spiral and straight flutes, to determine the
best tool for the specific job.
For more information, click on the author biography at the top of this page.
|