ROUTING: Routing & Trimming PET
PET (polyethylene
terephthalate)
is a popular
material for thermoforming.
PET can be formulated
several ways: x
as unreinforced, glass
fiber reinforced, other
reinforced and as PETG,
to name a few. Each of
these formulated materials
have unique characteristics
which may
require different cutting
tools, spindle speeds,
feed rates and fixturing
to optimize finish and
production rates. Unreinforced PET and PETG are flexible
materials that will flutter when machined if not fixtured
properly. All PET materials can be gummy yet tough and
require the less violent cutting action of an O flute router
bit. Do not use V or Z flute cutting tools with PET because
all grades are subject to crack propagation which will
occur more frequently with such geometry.
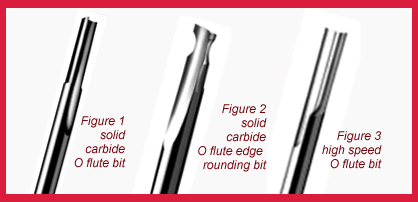
PET is used for POP displays, drafting templates, window
well covers, beverage centers, auto accessories and
many types of clear or see through covers. Routing these
products on a CNC router is best accomplished with
solid carbide single edge O flute router bits, such as the
one shown in Figure 1.
If a curved edge is required,
then a solid carbide
O flute edge rounding
bit as shown in Figure
2 is the best choice.
Both tools are also available
in a two flute configuration
which can be
tested if finish is a
problem with the single
flute tool.
If air routers are
being used to rout or
trim unreinforced PET
or PETG then high
speed steel O flute
router bits may be the most cost-effective choice. The
high speed O flute bit is shown in Figure 3. Solid carbide
O flute bits are also a good choice for air routers when
cutting all types of PET.
When programming a CNC router for cutting PET, there
are a few considerations that will dramatically affect production,
scrap and finish. Entry into the cut should be a
ramping and not plunging action. Outside or perimeter
sharp corners should be programmed as a loop or exit
ramp movement to prevent tool stops or dwells which can
cause crack propagation, heat or burning. Spindle speed
should be set at 18,000 rpm and feed rates between 200
to 350 inches per minute for 1/4” inch and below diameter
tools. PET should be cut as fast as possible with a one
pass cut. There is reasonably little experimenting to be
done other than finding the fastest speed rate when routing
PET materials once the right cutting tool has been
selected and proper programming techniques have been
employed.
For more information, click on the Author Biography at the top of this page.
|