Laser Processing of Plastic Sheet
When determining processing options for plastic sheet and non-conductive products, lasers offer the flexibility, precision and repeatability required to produce excellent results. Laser processing of plastic is accomplished by the absorption of highly-focused laser energy. The longer wavelength of the laser results in a conversion of light into heat. The heat generated through this process produces a selective vaporization and decomposition of the plastic to form an accurate cut.
Lasers are a fairly new technology. Recognized as a valuable tool in the late 1960s, lasers have become essential in processing for a wide range of industrial applications including automotive, aerospace, medical and manufacturing. Lasers emit light as an almost parallel, single color of light. The laser light is easily focused to a pre-determined spot and size that does not require the use of filters to provide the colored light needed for the job. In a comparison of a standard light bulb and laser, a 100-watt laser radiates the same total amount of energy as a 100-watt light bulb. However, the maximum energy density available from the laser is 10,000,000 times greater in a focused spot than the energy available from focusing the light bulb.
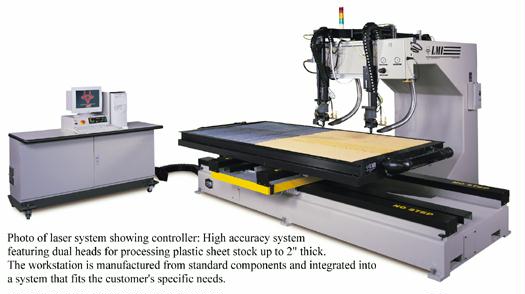
Industrial lasers allow a tremendous amount of energy to be focused on a small, well-defined spot. The laser heats, melts and/or vaporizes materials in the defined "spot", applying heat only where it is needed with a minimal heat-affected zone outside of the focused spot of energy.
The Basic Advantages Of Lasers
Lasers are a unique tool in that they offer creative manufacturing and problem-solving capabilities. Lasers add attributes to a product that may not be achieved through conventional methods.
The laser is a single point cutting source with a very small point (0.001 to 0.020 inch diameter) allowing for fine, precision cutting. Always sharp, lasers can easily process materials that may present problems when worked with traditional mechanical methods. The "forceless" nature of lasers permits fragile or thin materials to be processed with minimal support or tooling; and the flexibility of the laser allows intricate shapes and patterns to be cut or engraved without distortion. A cut pattern can also be quickly changed or adjusted simply by altering the program controls for the laser.
Plastics Processing By Lasers
The type of laser used primarily in the plastics industry is the CO2 laser. This means that CO2 is the specific gas used in the resonator to determine the wavelength of the laser light produced. CO2 lasers emit energy at 10.6 microns; a wavelength that is generally well absorbed by non-metal materials.
CO2 lasers are available in three main configurations: Slow flow; Fast axial flow and Sealed. The slow flow lasers are recognized as mature technology lasers which have been used on a consistent basis in the industry since about the mid-1970s. They are typically a continuous-wave laser; however, they may be electronically pulsed up to 2000Hz by turning the power supply on and off. Some CO2 lasers also have an "Enhanced Pulse" power supply design that allows up to five times or more the continuous wave power for 100 micro-seconds or more. A disadvantage of slow flow lasers is their design. They require a large footprint of space in order to achieve high power.
The Fast axial flow lasers overcome this disadvantage by utilizing a system of blowers to move the gas through the discharge regions and by cooling the gas with external heat exchangers. Fast flow lasers can achieve higher power (up to 600 watts/meters of length) and are the primary industrial laser in the 1-10 kw lasers.
Sealed lasers are fully contained units that run on gases. The gases necessary for the process are contained within the laser and are expendable. At the end of the life of the laser, it can be sent back to the manufacturer to be recharged.
Primary Considerations in Laser Processing
There are three main factors to consider in the laser processing of a specific material (see Figure 1).
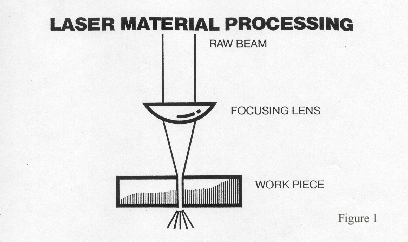
Absorption of Material.Materials are usually classified as reflective or transparent. Users need to determine how much energy will be absorbed by the material and how does this absorption rate vary with the temperature of the materials.
Thermal Diffusity.What is the speed at which the heat absorbed by the material is conducted away? This factor is a function of the thermal conductivity or the specific heat and/or thickness of a material.
Reaction Temperature. At what temperature does the material melt or vaporize; and how much heat is required to reach that temperature?
Secondary Considerations in Laser Processing
Heat-affected Zone. This zone refers to the material (as small as .001") which surrounds the laser-heated material. Depending on the type of material processed, this heat-affected zone may exhibit charring, hardening or flame polishing (see Figure 2).
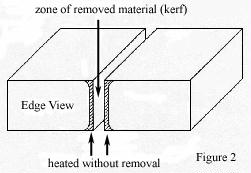
Smoke or Debris. As lasers cut, the material melts or vaporizes. The user must consider how to eliminate the smoke/debris residue produced from laser processing.
Burr or Dross on Edge. Some materials may exhibit a burr of melted material or a slag (dross) left on the edge after laser cutting.
Thermal Expansion. This factor may be a consideration when working with brittle materials such as ceramics or glass where the heat generated may cause expansion or cracking.
Dissimilar Materials. Special consideration is required for combinations of materials because they may have different thermal characteristics.
Tolerances. Since there is no well-defined edge to the laser beam, squareness specifications, profile and thickness of cut need to be considered. Laser cutting has basically a .001" tolerance. Smaller tolerance levels may be achieved during laser processing, however several factors such as material properties, laser and beam parameters and equipment design must be considered.
Reaction Properties and Personal Safety. The reaction properties generated during the laser processing must be determined and analyzed for human safety.
Safety. A primary concern is eye safety; however the high-energy beam can also seriously cut or burn. Other factors to consider are the type of laser (Class I or Class IV), energy level, wavelength and the amount of training personnel have received.
Assist Gases. The operator needs to determine what gas to use in processing to help oxidize the material or to protect against oxidation.
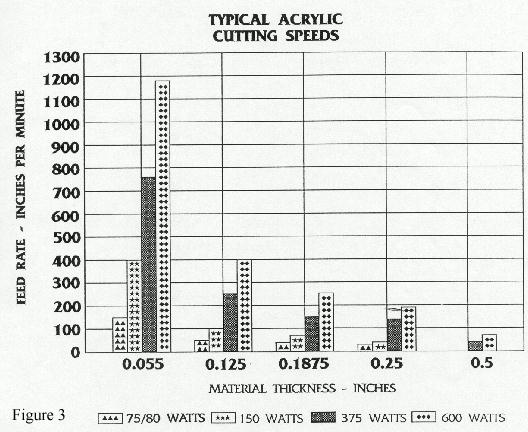
Basic Rules Affecting Cut Quality
There are several factors that determine the cut quality of a specific material. The basic rules are as follows:
The Edge Finish. The edge finish of a material depends primarily on its reaction to the laser energy. Plastic and non-conductive materials are generally divided into three catagories:
•
Materials which cut easily with no discoloration: typically cutting is accomplished through Vaporization.
Note: There are no thermosets in this category.
Acrylics |
Polypropylene |
Polyethylene |
Polystyrene |
•
Materials which exhibit some discoloration. This category includes materials that range from no discoloration to a high degree of heat affected zone: cutting is accomplished through Melt Shearing.
Note: There may be some thermosets in this category.
Acetal |
PETG |
Cellulosics |
Polyester |
ABS |
Polysolfene |
Floropolymers |
Silicones |
Nylons |
Polyurethane |
•
Materials that always result in some degree of discolored edge: cutting is typically accomplished through Chemical Degradation.
Note: This category includes thermosets and high-temperature materials.
Allyd |
Polyamide-imide |
Allyl |
Polycarbonate |
Amino |
Polyimide |
Epoxys |
Polyphenylene sulfide |
Memaines |
PVC |
Phelnolics |
|
Thickness of Material. Thicker material typically equals a lower quality cut. For example, polycarbonate that is .060" thick will display a slight brown-colored edge when cut at 400 watts, however; at .375" thick, the edge will be almost black in color.
Power Variations. Plastics and non-conductive products are sensitive to power variations. To avoid creating grooves in the material, power must be reduced at corners or at stops between the segments.
Beam Quality. The laser beam quality must be uniform or fringes/steps will appear as lines/ledges on the finished cut edge.

High-Energy Density Beams. A higher energy density laser beam and a more clearly defined edge of the beam result in a higher quality cut.
Speed of Cut. The faster the speed of the laser generally produces a higher quality of edge cut.
Exhaust of Smoke and Vapor . To achieve a clean cut edge, consistent exhausting of the residue smoke and vapor from the laser process is required. The user must also be aware of airflow to prevent discoloration of the cut area.
In the laser processing of plastic sheets, the keys to quality are as follows; (1) the controller, (2) the motion system, (3) the laser and beam delivery combined with, (4) the reactive elements of the material.
Written by Tim Christopherson, Manager Non-Metals Market for Laser Machining, Inc., manufacturers of Integrated laser processing systems both standard and custom engineered. References:
Lawson, William E. "Laser Processing of Materials and Plastics." Laser Machining, Inc., 1994.
Powell, John "LIA Handbook of Laser Materials Processing," 2001.
For more information, contact Mr. Christopherson at Laser Machining, Inc., 500 Laser Drive, Somerset, WI 54025, 800-775-2737 ext. 1125, Fax: 715-247-5650, E-mail: tchris@lasermachining.com, Web: www.lasermachining.com.
|