PLASTIC WELDING: Considerations for the Proper Handling of Welders Life is not perfect. I guess everybody knows this by now. If you work in ‘Real-life’ situations you will find that a perfect workspace is not available most of the time. Sure, if you could work in your shop with all your equipment and tools, a good ventilation system, a workbench with all the fixtures and the right position for the parts and yourself, good illumination the entire time etc., this would be ideal. But keep in mind that life is not always the way we wish it to be. More than likely you will find yourself in situations where the weld area is difficult to reach and even located in dark and tight spaces. Areas might be contaminated with mediums that are harmful, requiring you to wear special protection, which also makes it difficult to move and/or will decrease your field of view. Often a ladder or a safety harness may be required to reach areas that are high up. When you have to work inside a tank or directly under the ceiling for example, this will put you in an unstable posture.
When a welding operation combines shop welds, as well as, field-welds, it is recommended to make as many welds as possible in the shop, because the conditions are easier to control. Unknown situations in the field may bring unwanted difficulties and costs. Take some time to plan ahead. Plan your job step by step. Sure this takes some time in the beginning, but it will save time and money in the end. You will find that a well-planned job will reduce the costs for special tools or other equipment as well as for the working time.
In order to provide a quality weld, the welding operations rely mostly on the skills of the operator. Therefore he/she is responsible for the delivered quality of the product.
To keep the welder in the right position and to bring the necessary pressure on the welding rod can be challenging in circumstances like those above. As soon as you apply pressure while hanging in a safety harness or standing on a ladder, you get pushed back. It’s like sitting in a swing.
Another difficulty occurs when a welding job needs to be done in a bigger pipe or a small box. Maybe you have to lay down, weld overhead or in another uncomfortable position. The right position of the welder to the material that needs to be welded is important. It does not matter what kind of welding system you use - the wrong position will decrease the quality of your weld enormously. Remember the three welding parameters: Temperature, Pressure and Time. Is the preheat unit pointed to the needed zone in front of the welding rod? If the distance is too far or too close, the weld will be cold or too hot. When the pressure is too low, because you are not able to apply enough of it to the material, you will run into some problems there as well. This scenario will mostly happen with hot air and extrusion welders. These units are most commonly used in repairs and fabrication jobs. Some large extrusion welders are quite heavy - up to 37 lbs. (17 kg) and more, others are smaller and lighter. The big and heavy welders (depending on the job) need a support to composite the weight. This makes it difficult to reach certain areas and you may tire after a short while. Spending some time in advance thinking about the best weld design can help prevent some of these problems and potential costs.
So called "stick welders" require a lot of skills right from the beginning. The preparation of the weld area and the welding rod has to be done the proper way (see previous articles on our website at www.plasticsmag.com). The pressure is very hard to control with these units because the touch of the person who makes the weld is what applies the pressure. The distance of the welder’s nozzle to the welding rod has to be constant. The welding rod will melt faster than the parent material. For this reason a larger area of the parent material needs to be preheated. Approximately ½" of the welding rod length and 1" in length of the parent material is appropriate. The welder motion should be done in a fanning kind of way, while the welding rod is in a straight 90º angle (see image below). The 90º angle is to be used with harder plastic materials. The angle will change with softer rod materials. But be careful, if the angle is too flat, because you want to be a little bit faster or the room you have to work in is not high enough, the welding rod material will be stretched and the risk of tearing-off the welding rod is possible.
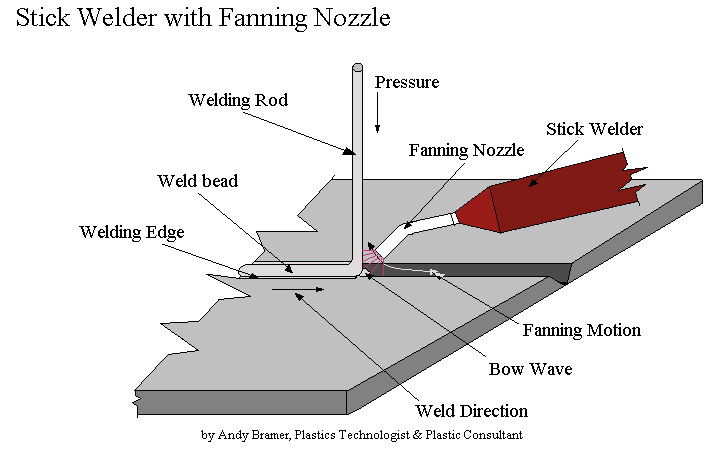
Welding with a stick welder and a "speed welding nozzle" (see image below) might be faster, but for some materials a special feeling for the material is necessary. PE and PP are, compared to PVC for example, fairly easy to weld with this nozzle type, while PVC requires more skill. Because the pre-heat zone inside the nozzle is quite large, the welding rod will melt faster than with a fanning nozzle. The rod gets soft in a shorter time and could bend and stick inside the nozzle. The whole welding process can be done in a shorter time. Again, the quality depends on the skills and knowledge of the operator.
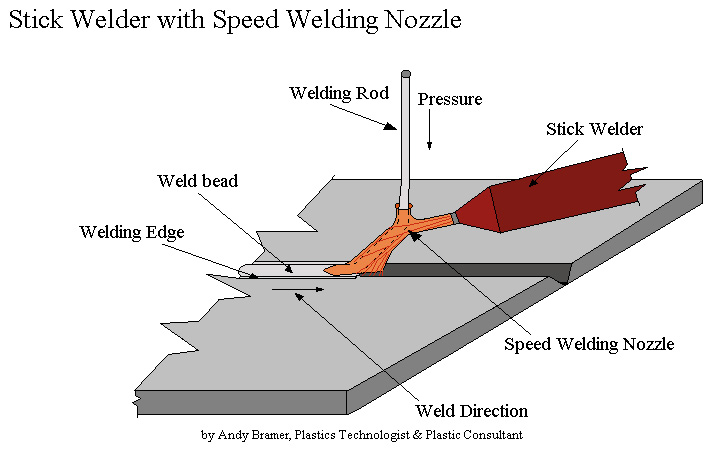
With both stick welder systems, the operator must use both hands in order to move the welder and apply the pressure to the welding rod. The handling of larger extrusion welders is a different issue. These units are much bigger and heavier than stick- or injection welders. Their use is to provide a large weld bead for heavy construction. Again, the use for these machines needs to be taught and instructed by a person who knows how this large equipment is to be used. Many different sizes of extrusion welders can be found on the market today. Basically the welder position should be downwards to use the weight of the machine to apply some of the required pressure. As we know life is not always what the doctor ordered. Some times the welder needs to be lifted up. A support will help to reduce some of the welder’s weight. This, however, could cause problems if the weld area is not easy to access.
Injection welders (see sketch below) have other advantages versus these other systems. First, their use is fairly easy and the weld quality is typically very high. Second, you can weld different bead sizes by changing the aluminum tip to the proportions you need to weld. Weld areas are easy to reach because of the relatively small welder size.
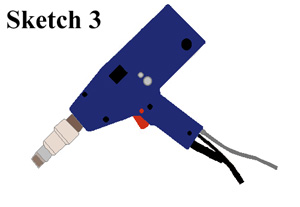
For hot plate welding it is required that the two welded parts have the same shape. If a hot plate weld has to be done, e.g. in pipeline joints, the earlier mentioned parameters will apply for this kind of welding as well. I can not stress this enough, it does not matter what kind of welding equipment you have in use, temperature, pressure and time are always important. You can find parameter charts for hot plate welding for the right temperature, the right pressure and the right times. If you have problems finding them, please contact me. The parameters depend on the material, wall thickness and diameter (or size). The parameter charts will refer to the welding process, which is illustrated below.
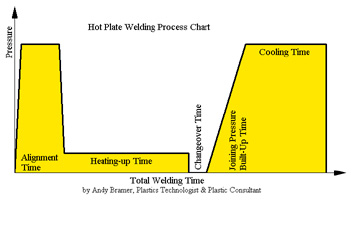
It is essential to have employees educated in plastic welding performing the weld jobs if you wish to achieve quality welds. Plastic welding looks easy, but if you do not understand the importance of all the parameters, preparations, and exercises, it can be difficult to achieve quality welds. Therefore, I highly recommend spending some time and money on training. Please, feel free to contact me for more information on a One-Day Plastic-Welding Seminar I offer in Edmonton, AB Canada. Other manufacturers and reps also offer courses. Whichever you choose, proper training will increase the efficiency and quality of your welded products and the satisfaction of your customers.
For past Plastic Welding articles in this series, see our website at www.plasticsmag.com and click on Plastic Welding under "Series". As always, we want to hear from you. Send your questions care of the magazine or e-mail me at abramer@drader.com.
For more information, click on the Author Biography link at the top of this page.
|